Laser-interferometric Length Measurement Tracking System
Introduction
This study deals with a two-degree-of-freedom special manipulator for tilting a set of a laser light source and a detector around two axes. Six sets of this manipulator is planned for feedback sensors to measure six-degree-of-freedom relative motions between a tool spindle and surface plate of a precision machine tool or a coordinate measuring machine. Each laser tracker consists of a laser-interferometric length measurement sensor and a 2-degree-of-freedom parallel kinematic manipulator driven by two VCM linear actuators.

Figure 1 Fundamentals of proposed machine system based on 6-DOF measurement device between tool and workpiece
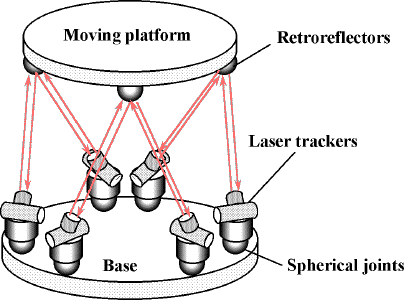
Figure 2 Six-DOF motion measurement device consisting of six laser interferometry-based trackers
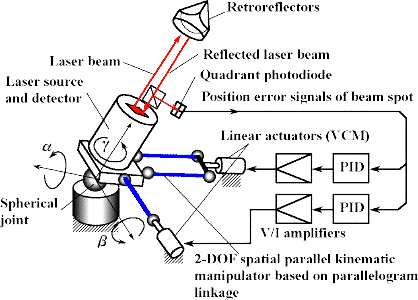
Figure 3 Laser tracker based on two-DOF spatial parallel kinematic manipulator actuated by two linear voice coil motors
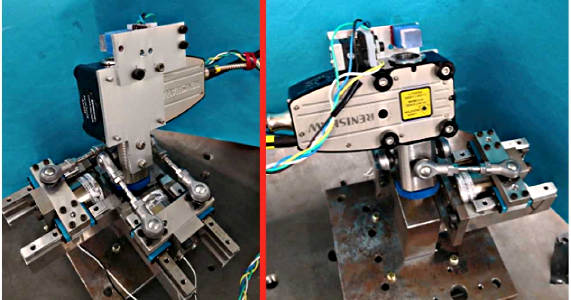
Figure 3 Laser tracker based on two-DOF spatial parallel kinematic manipulator actuated by two linear voice coil motors
Proceedings
- Baris Celik, Takaaki Oiwa and Junichi Asama: Design and Development of Two-degree-of-freedom Parallel Manipulator for Tilting Laser Interferometry Tracking System,
The 7th International Conference of Asian Society for Precision Engineering and Nanotechnology(ASPEN2017), Seoul, Korea Nov.16, 2017.
- Baris Celik, Takaaki Oiwa, Kenji.Terabayashi1 and Junichi Asama:Two-degree-of-freedom special parallel manipulator for laser interferometry-based tracker,
The Fourth Conference on Mechanisms, Transmissions and Applications(MeTrApp2017), Trabzon, Turkey, July 3-5, 2017.
To Oiwa laboratory
Copyright (C) 1997 OIWA Laboratory All Rights Reserved.