Ultra-precise Machine System with 6-DOF Perfect Motion between Tool and Workpiece
This study proposes a compensation system for 6-DOF motion errors between the end-effector and the workpiece. A hexapod-type parallel mechanism with 6 passive prismatic joints measures 6-DOF motions to compensate for the end-effector's position errors independently of the temperature fluctuation and external forces.
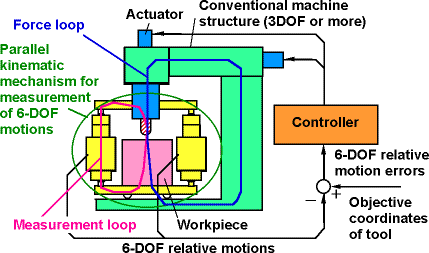
Figure Ultra-precise machine system using Hexapod-type measurement device
To realize an ultra-precise machine, a mechanism which generates high relative motion between its tool and the workpiece is required as well as the accuracy improvements of each element of the machine. This study presents a compensation system for 6-DOF errors between the tool and the workpiece in machine tools and coordinate measuring machines. A hexapod-type parallel mechanism installed between the tool spindle and the surface plate measures 6-DOF motions regardless with the temperature fluctuation and external force. Moreover, the tool position errors are compensated.
In this machine system, the measurement system is separated from the structural frame. This is based on "the metrology frame architecture" proposed by Prof. Bryan in 1989.
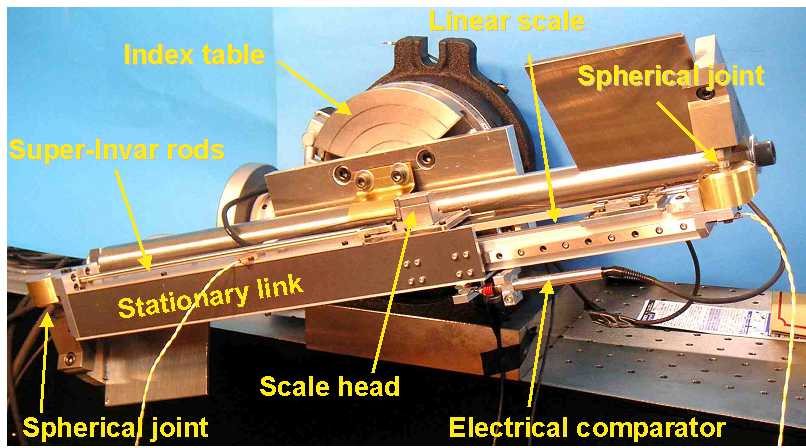
Figure A passively-extensible strut consisting of two spherical joints and one prismatic joint with a linear scale unit. This strut has special compensation system for elastic and thermal deformations of joints and links.
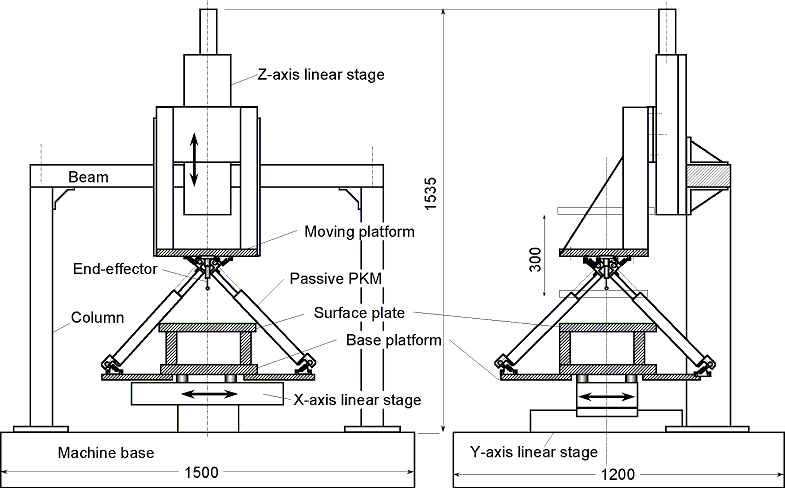
Figure An experimental machine consisting of an XYZ mechanism and a passive hexapod mechanism (under construction at present)
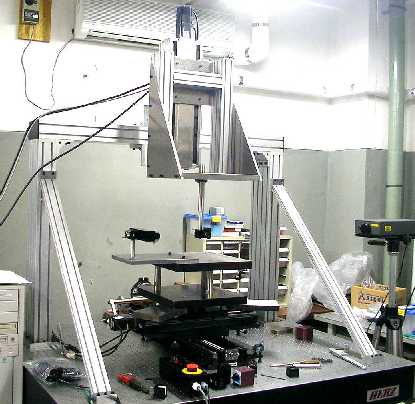
Figure An experimental machine consisting of an XYZ mechanism and a passive hexapod mechanism (under construction at present)
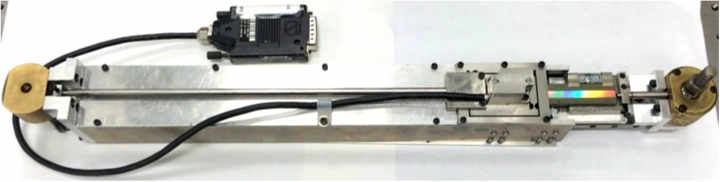
Figure An extensible strut equipped with a linear encoder with measuring range of 270 mm
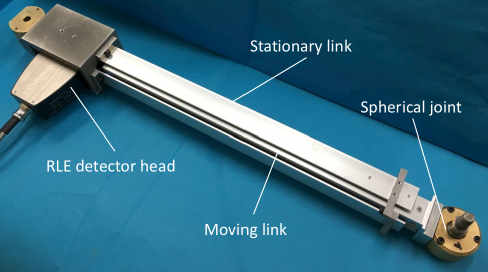
Figure An extensible strut equipped with a laser interferometric length measuring system
References
Papers
-
Takaaki OIWA: An Ultraprecise Machining System with a Hexapod Device to Measure Six-Degree-Of-Freedom Relative Motions Between The Tool And Workpiece, International Journal of Precision Engineering and Manufacturing, Vol.8 No.2 Apr 2007 pp.3-8.
Proceedings
- Baris Celik, Takaaki Oiwa and Junichi Asama: Design and Development of Two-degree-of-freedom Parallel Manipulator for Tilting Laser Interferometry Tracking System,
The 7th International Conference of Asian Society for Precision Engineering and Nanotechnology(ASPEN2017), Seoul, Korea Nov.16, 2017.
- Baris Celik, Takaaki Oiwa, Kenji.Terabayashi1 and Junichi Asama:Two-degree-of-freedom special parallel manipulator for laser interferometry-based tracker,
The Fourth Conference on Mechanisms, Transmissions and Applications(MeTrApp2017), Trabzon, Turkey, July 3-5, 2017.
- Yukio NAKAZAWA, Takaaki OIWA, Kenji TERABAYASHI and Junichi ASAMA: Measurement stability improvement of passive extendable strut equipped with laser interferometer length measurement system,
16th International Conference on Precision Engineering(ICPE2016),Hamamatsu, Japan P03-8160.
- Yukio NAKAZAWA, Takaaki OIWA, Kenji TERABAYASHI and Junichi ASAMA: Measurement stability improvement of passive extendable strut equipped with laser interferometer length measurement system,
The 7th International Conference on Positioning Technology (ICPT 2016),Seoul, Korea, p49, Nov.8-11, 2016.
- Takaaki Oiwa, Kazuki Kobayashi, Kenji Terabayashiand Junichi Asama:
A Precision Machine System with Hexapod Device to Measure Six-degree-of-freedom Relative Motions between Tool and Workpiece,
The 19th International Conference on Mechatronics Technology ICMT2015, November27-30, 2015, Tokyo, Japan.
- Takaaki Oiwa, Kazuki Kobayashi, Kenji Terabayashiand Junichi Asama:
Ultra-precision machine system feedback-controlled with hexapod-type measurement device for six-degree-of-freedom relative motions between tool and workpiece
Mechatronics2015,Warsaw, Poland, Sep. 21-23, 2015.
- Kazuki KOBAYASHI, Takaaki OIWA, Junichi ASAMA and Kenji TERABAYASHI:
Investigation on accuracy improvement in hexapod-type measurement device for six degree-of-freedom relative motions (P2-29MS),
, pp434-436,
The 6th International Conference on Positioning Technology ICPT2014, Nov. 18-21, 2014, Kitakyushu International Conference Center, Kitakyushu-shi, Fukuoka, Japan.
- Takaaki OIWA, WenBo YAO and Junichi ASAMA: Ultra-precision machine system feedback-controlled using hexapod-type measurement device for six-degree-of-freedom relative motions between tool and workpiece,
euspen Lamdamap 10th International Conference, 20th-21st March, 2013,Kavli Royal Society International Centre, Buckinghamshire, UK
- Takaaki Oiwa:
Ultra-precision machine feedback-controlled using hexapod-type measurement device for six-degree-of-freedom relative motions between tool and workpiece,
7th International Conference Mechatronics 2007, (2007.9) Warsaw, Poland.
- Takaaki Oiwa:
Ultra-precision machine tool or coordinate measuring machine using hexapod-type measurement device for six degree-of-freedom relative motions between cutting tool/probe and workpiece, 12th IFToMM world congress, (2007.6) Besancon, France.
- Takaaki Oiwa:
Ultra-precise machine with six-degree-of-freedom perfect relative motion between tool and workpiece,
International Symposium on Flexible Automation, (2006.7) Osaka.
- Takaaki Oiwa:
Ultra-precise Machine System Using Hexapod-type Measurement Device for Six-Degree-of-Freedom Relative Motions Between Tool and Workpiece,
Proceedings of the 5th Chemnitz Parallel Kinematics Seminar, (April 25-26, 2006 Chemnitz, Germany)
- Takaaki Oiwa:
Ultra-precise Machine with 6-DOF Perfect Relative Motion between Tool and Workpiece,
KSME-JSME Joint Int. Conf. on Manufacturing, Machine Design and Tribplogy, (June 23, 2005 Korea, Seoul) DLM-305-1-4.
- Takaaki OIWA:
Ultra-precise Machine with 6 DOF Perfect Relative Motion between Tool and Workpiece,
Autumn meeting of JSPE, 2004, pp.869-870D
To Oiwa laboratory
Copyright (C) 1997 OIWA Laboratory All Rights Reserved.