Optimum design for Ultra Precision Mechanism
-Shape Optimization for Flexure Hinges-
@@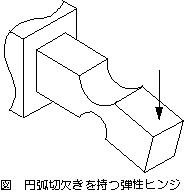
Shape Optimization for Flexure Hinges
Takaaki OIWA and Toshihiko SUGIMOTO
Abstract
The purpose of this study is to design an optimum profile of the flexure hinge with high axial stiffness and high bending flexibility. The conventional circular notched and rectangular notched profiles are not optimum because of low flexibility and high stress concentration. In this paper, the optimum profile with uniform stress distribution was generated using the finite element method under constraint conditions which unify the axial stiffness and minimum thickness of the notched profiles. Moreover, the flexibility of the optimum profile was compared with the flexibility of ellipse profiles, round rectangular profiles and profiles described by higher degree functions. As a result, the optimum profile had flatter stress distribution and the highest flexibility under a maximum stress constraint condition. The optimum hinge has 19% higher bending compliance than the conventional circular notched hinge, and produces 67% higher deflection angle than the rectangular notched hinge.
Key words: flexure hinges, hinge profile, bending elastic hinges, optimum design, flexibility
Fig. Stress distribution of circular arc flexure hinge
Fig. Strees distribution of rentangle flexure hinge
Fig. Stress distribution of optimum shaped flexure hinge
-Torsional Elastic Hinge-
A Study on Torsional Elastic Hinge
Takaaki OIWA and Takahiro MATSUNAGA
Abstract
This paper deals with the optimum design of the torsional elastic hinge instead of the flexure hinge used as the revolutionary joint of the precise mechanism. Influence of the torsion beam dimensions on the flexural stiffness and torsional compliance of the hinge is investigated by using the finite element method, and the stiffness is compared with that of the conventional circular notched flexure hinge. As a result, the torsional hinge with the same stiffness as the flexure hinge has several times higher rotational angle under a maximum stress constraint condition. A displacement amplifier with the torsional hinge shows that the measured stiffness agrees with the calculated result, and the magnifying efficiency is 86%. By notching to the torsion beam center, the ratio of the flexural stiffness to the torsional stiffness has increased 55%, and the rotational angle has increased 19%.
Key words: torsional elastic hinge, flexure hinge, flexural stiffness, torsional compliance, rotational angle, finite element method
Fig. Proposed torsion beam type hinge
Fig. Finite element mesh of torsion beam hinge
References
Takaaki OIWA and Takahiro MATSUNAGA
A Study on Torsional Elastic Hinge
J. Jpn. Soc. Prec. Eng.,
Vol. 63, No. 10 (1997)pp.1454-1458.(in Japanese)
Takaaki OIWA and Toshihiko SUGIMOTO
Shape Optimization for Flexure Hinges
J. Jpn. Soc. Prec. Eng.,
Vol. 66, No. 60 (2000) pp.955-959.(in Japanese)
To OIWA Laboratoly
Copyright (C) 1997 OIWA Laboratory All Rights Reserved.